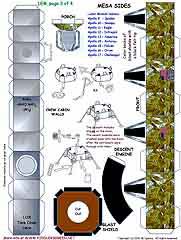
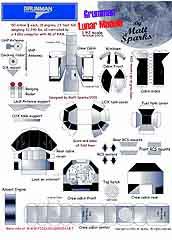
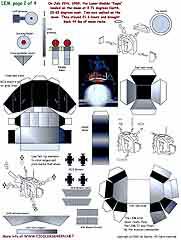
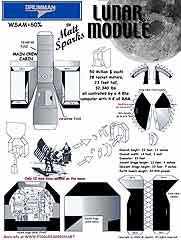
The Grumman LEM- Lunar Excursion Module
This Module is also known as the Lunar Module or "LM".
Matt lives in Colfax Ca in the Sierra foothills and works his day job at McClatchy Publishers (Sacramento Bee) as the IT Coordinator.
He co-designed the Colditz Prison Escape with Chip.
Matt has chosen to include the instructions along with the actual LEM model...
Just when I thought FG couldn't get any better...
All I can say is "Wow!" You guys just keep turning out great stuff! I'm starting the Mercury capsule tomorrow and can hardly wait for the LEM. After discovering paper modeling and FG, I wanted to find a paper LEM model but couldn't. I even considered trying my hand at designing (something "simple" like the LEM! HA!) but now I see "I'm not worthy..." Maybe someday. Sincerely, J.H.
Lunar Excursion Module by Grumman
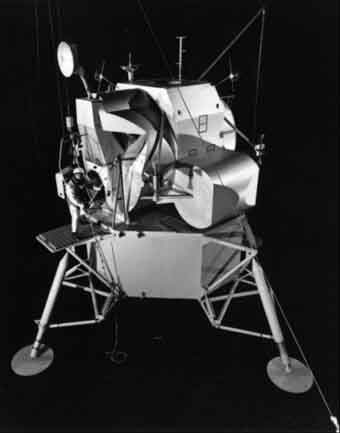
In the aftermath of Gagarin's flight, President Kennedy asked Vice President Johnson to find a way to regain American technological prestige through space flight. NASA top management was in almost constant communication with the White House staff, Bureau of the Budget officials, and congressional leaders. Apollo was about to pass from planning to action. Less than a month and a half after the Russian feat, NASA's new manned space flight project was approved.
Now it is time to take longer strides - time for a great
new American enterprise - time for this nation to take a clearly
leading role in space achievement, which in many ways may hold
the key to our future on earth.
. . I believe that this nation should commit itself to achieving the goal, before this decade is out, of landing a man on the moon and returning him safely to the earth. No single space project in this period will be more impressive to mankind, or more important for the long-range exploration of space; and none will be so difficult or expensive to accomplish.
With these words, on 25 May 1961, President Kennedy proclaimed before Congress and the world that manned lunar landing belonged in the forefront of an expanded American space program.73 And Congress obviously agreed with him. With almost no internal opposition, both the Senate and the House of Representatives responded to Kennedy's challenge by increasing funds for the agency that was to undertake this bold program. At this juncture, the Americans had chalked up 15 minutes and 22 seconds of manned space flight experience. The Russians had clocked 108 minutes.
On 5 May 1961, NASA had launched Freedom 7, the
first manned U.S. spacecraft. Pilot Alan Shepard became the forerunner
of a new genre of American adventurer-hero, the astronaut.* Shepard's
flight, a lob shot up over the Atlantic, was a far from spectacular
demonstration of this country's space faring capabilities when
compared to Gagarin's single orbit of the earth. But, as only
the third flight of a Mercury-Redstone, it was a dangerous
and daring feat.
![]() |
NASA officials maintained that the agency was ready and eager to take on the lunar landing, even though it added enormously to the challenge of Apollo. Following the President's speech on 25 May, Webb, Dryden, and Seaman's told newsmen that much of the additional funding Kennedy had requested would be spent on advanced launch vehicles, particularly Nova, the key to manned lunar landings. Nova was so crucial to Apollo, Webb declared, that the agency planned a parallel approach to the development of propellants for the big booster. NASA would continue its work on liquid propellants, while the Department of Defense would pursue solid-fueled-rocket development as an alternative for Nova's first stage. "As soon as the technical promise of each approach can be adequately assessed," he said, "one will be selected for final development and utilization in the manned space program."
![]() |
Dryden expanded on Webb's statement. Asked if the agency considered orbital rendezvous a serious alternative to use of Nova, he replied, "We are still studying that, but we do not believe at this time that we could rely on [it]." He stressed that Kennedy's decision had forced NASA to begin work on Nova prematurely:
This illustrates the real nature of the decision. We could make some of these decisions better two years from now than we can now, if the program had gone along at the ordinary pace. But if we are going to accelerate this we have got to do some parallel approaches, at least for a time. The solid and the liquid propellant are going to be carried forward full steam. We have a certain amount of effort on rendezvous. If it looks like this presents any opportunity, we will certainly take advantage of it.76
Both Dryden and Seaman's freely admitted that NASA lacked the immediate scientific knowledge needed for lunar landings. Another use of the additional funding would be to speed up research into the unknowns. Development of hardware - boosters, spacecraft, and equipment - must be built upon this scientific and technical foundation. At this juncture, nobody had any really firm idea about how NASA was going to implement Kennedy's decision. Techniques for leaving the earth and flying to the moon - even more, landing there and returning - were open to considerable debate and much speculation.
![]() |
![]() |
![]() |
![]() |
![]() |
Question about how Matt got the crinkly
effect on the LEM .. The top (ascent stage) was made of sheet aluminum (actually coated stuff) The bottom (descent stage) was covered with Kapton Film (a gold colored Mylar type stuff)The bottom was crinkly and gold, the top was silver and flat I guess I better go with the flat silver. I will work on the highlights on the panels and stuff. I got the effect easy, I stole it from RM... :) he took a digital picture of aluminum foil and colored it gold. I just grayscale it silver for the top and used it as is for the bottom. Matt |
There was a vague feeling within the agency (though with several notable exceptions) that direct ascent would eventually be the answer, but no one had worked out the tradeoffs in much detail. Subsequently, as Apollo planning progressed, the question of how to fly to the moon and back loomed ever larger. In the end, the choice of mode was perhaps the single greatest technical decision of the entire Apollo program.
The selection was inextricably linked to launch vehicles, spacecraft, facilities, cost, development schedules, and the future of America's posture in space. Ultimately, the mode question shaped the whole of Apollo. Many possible methods were carefully considered, and a Pandora's box of problems was opened.
At the time, however, technical thinking had not matured to that degree. The United States was just on the threshold of manned space flight, and orbital flights around the earth were in themselves mind-boggling. A program to land men on the moon, 400,000 kilometers away, and bring them safely home was nearly too stupendous for serious contemplation.
Hatches and Landing Gear
The lander originally had two docking hatches, one at the top center of the cabin and another in the forward position, or nose, of the vehicle, with a tunnel in each location to permit astronauts to crawl from one pressurized vehicle to the other. (Extravehicular transfer between craft remained an emergency backup method.) After injection into a trans lunar trajectory, a course toward the moon, the command module pilot would turn his ship around, fly up to and dock with the lander's upper hatch, and then back the two vehicles away from the spent S-IVB third stage. This top-to-top docking arrangement aligned the thrust vector of the service module propulsion engine with the centers of gravity of the two spacecraft, thus avoiding adverse torques or tendencies to tumble during firings for midcourse corrections and injection into lunar orbit. The crew would enter the lunar module through this hatch. When the lander returned from the moon, however, the front hatch would be used for docking and crew transfer. With no windows in the top of the lander, the lunar pilots would be flying blind if they docked with the upper hatch. One of Grumman's human factor experts later said, in an apt analogy, "It's nice to see the garage . . . when you drive into it."
By spring 1964, NASA and Grumman engineers were thinking of deleting the front docking procedure and adding a small window above the lunar module commander's head. This overhead window might add seven kilograms weight and some extra thermal burden, but cabin redesign would be minimal. The added weight would be offset by eliminating the front tunnel and the extra structural strength needed to withstand impact loads in two areas. Eliminating forward docking had another advantage. The hatches could now be designed for a single purpose - access to the command module through one hatch and to the lunar surface through the other - which certainly simplified the design of the forward hatch. NASA directed Grumman to remove the forward docking interface but to leave the hatch for the astronauts to use as a door while on the moon.
Once the location of the hatches was settled, getting the astronauts out and onto the lunar surface had to be investigated. Using a cable contraption called a "Peter Pan rig" to simulate the moon's gravity, Grumman technicians looked into ways for the crews to lower themselves to the lunar surface and to climb back into the spacecraft. When astronaut Edward White, among others, scrambled around a mockup of the lander, using a block and tackle arrangement and a simple knotted rope, he found that both were impractical. In mid-1964 a porch, or ledge, was installed outside the hatch and a ladder and handrail on the forward landing gear leg. When the astronauts discovered they had trouble squeezing through the round hatch in their pressurized suits and wearing the bulky back pads, the hatch was squared off to permit easier passage.
Astronauts found a knotted rope from the lunar module difficult to climb down (or up) The addition of a ladder on a landing gear leg made the task much easier.
All these design features, although unusual, appeared to be compatible with the lunar environment - at least the engineers did not entertain any special worries. But the landing gear was different. The design of the legs and foot pads depended on assumptions about the nature and characteristics of the lunar surface. In the absence of any firm knowledge and with scientific authorities differing radically in their theories, how should one design legs to support a craft landing on the moon?
Grumman had first considered five legs but, during 1963, decided on four. The change was dictated by the weight-versus-strength tradeoff that had produced the cruciform descent stage, with its four obvious attachment points. The revised gear pattern also greatly simplified the structural mounting of the vehicle within the adapter. Four legs set on the orthogonal axes of the lander (forward, aft, left, and right) mated ideally with the pattern of four reaction control "quads" (the basic four-engine package). The quads were rotated 45 degrees so the downward-thrusting attitude control engine fired between the two nearest gear legs, overcoming a severe thermal problem of the five-leg arrangement.
While Bethpage was wrestling with the legs, Houston decided it had been too optimistic about the load-bearing strength of the lunar surface in the request for proposals. The resulting revision placed heavier demands on the landing gear, and Grumman had to enlarge the foot pads from 22 to 91 centimeters in diameter. The bigger feet made the gear too large to fit into the adapter. A retractable gear therefore replaced the simpler fixed-leg gear. Retractability also figured in the shift from five to four legs - the fewer to fold, the better.
Yep it's two pages now.
I am going to try to make it 3 inches even, |
|
The fit of the LM inside the adapter during launch.
Leg experts at Grumman had to change the geometry of the undercarriage, devise the best structure for impact absorption and stability upon landing, and choose the most suitable folding linkages. A broad program of computer-assisted analysis at Houston and Bethpage was used to determine the worst combinations of conditions at impact. The studies were reinforced by drop tests of lander models at Houston, Bethpage, and Langley. There were also plans to drop-test full-sized test articles to check out the new designs.
During 1963 Grumman engineers continued to worry about the nature of the lunar surface and to carry on theoretical and simulation studies of lunar geology and soil mechanics, with the support of such consulting firms as the Stevens Institute of Technology in New York and the Arthur D. Little Company in Massachusetts. Much of this work covered the interaction between vehicle and surface at the moment of landing. What would happen to the landing gear at touchdown? Would the lunar dust that might be kicked up by the descent engine exhaust obscure the landing site? Would soil erosion affect the stability of the lander? Washington also assisted in this research. In mid-1963, Bellcomm surveyed all that was being done inside and outside NASA and suggested that a backup gear be developed, in case the surface should be more inhospitable than it appeared.
But Grumman could not wait on the outcome of these studies. At meetings in Houston in October and November, contractor engineers described gears that tucked sideways (lateral folding) for stowage in the adapter; a tripod arrangement (radial), with three struts meeting at the base just above the footpad, that tucked inward; and a cantilevered device, with secondary struts for extra strength that folded inward against the vehicle for stowage and braced the leg when deployed for landing. Houston and Bethpage selected the cantilevered version. Somewhat narrower than the radial one, it was, in many ways, more stable. It had other advantages: less weight, shorter length for easier stowage, and a simpler, and therefore more reliable, folding mechanism.
A landing gear for the lunar surface had to be designed for varying landing conditions, such as protuberances, depressions, small craters, slopes, and soil-bearing strength. To achieve the necessary stability, the landing gear had to be able to absorb a diversity of impact loads. Houston and Bethpage met this challenge by using crushable honeycomb material in the struts, so the gear would compress on impact. A principal advantage of honeycomb shock absorbers was their simplicity. Since they had to work only once, the more common hydraulic shock absorbers and their complexities could be avoided. Subsequently, crushable honeycomb was also applied to the large saucer like foot pads to improve stability further for landing.
Specifications for the Grumman LEM
Ascent Stage | Decent Stage |
Crew: 2 |
Height minus landing probes:
8.59 feet |